ELYTT ENERGY develops the tooling to manufacture powerful ITER magnets
ELYTT ENERGY develops the tooling to manufacture powerful ITER magnets
A consortium leading by ELYTT ENERGY with ALSYOM and SEIV has signed a contract with Fusion for Energy (F4E), the EU organisation managing Europe’s contribution to ITER, for the supply of the handling and impregnation tooling required for the production of the PF coil magnets. The works will be completed in eight years and their value will be in the range of 30 million EUR. Johannes Schwemmer, F4E Director, explained that “This contract opens a brand new chapter for the European contribution to ITER magnets. The solid expertise of our contractors in the fields of engineering will be deployed to help us manufacture magnets of unprecedented size and complexity”. For Julio Lucas, Technical Director of ELYTT ENERGY, “This contract is a milestone for our company supplying high technology components and services. Together with our collaborators, we feel very proud and honoured that our work is going to contribute to the development of a future inexhaustible energy source for all mankind”.
The ITER Poloidal Field Coils
The poloidal field (PF) magnets pinch the plasma away from the walls and contribute in this way to maintaining the plasma’s shape and stability. The poloidal field is induced both by the magnets and by the current drive in the plasma itself.
The poloidal field coil system consists of six horizontal coils placed outside the toroidal magnet structure. The outer diameters of the PF2-PF5 Coils are between 17 and 25 metres and their weights range between 208 tons and 384 tons.
The ITER poloidal field coils are also made of cable-in-conduit conductors. Two different types of strands are used according to operating requirements, each displaying differences in high-current and high-temperature behaviour.
Each coil is based on a stack of multiple pancake winding units that minimizes joints. A glass-polyimide electrical insulation, impregnated with epoxy resin, gives a high voltage operating capability, tested up to 29 kV. The conductor jacket material has to resist the large electromagnetic forces arising during operation and be able to demonstrate good fatigue behaviour. The conductor will be produced in unit lengths up to 910 metres.
The scope of the contract
Initially through this contract, design and manufacturing studies will be carried out to develop the design. Then, the tooling will be manufactured and tested by the ELYTT ENERGY, before being finally shipped, assembled, commissioned and tested at the premises of the PF coils facility. Mechanical equipment will be developed that will lift, insulate and stack the layers of conductor. The impregnation tooling will conclude the electrical insulation of the coils by applying a vacuum, following by injecting and then curing resin in the coil. Last but not least, a gantry crane able to lift a load of 400 tonnes will be installed together with a set of stations for the final assembly of the coils.
Strong quality requirements are applied following ISO 9001, following a dedicated manufacturing plan, with the development of technical specifications, manufacturing procedures, control plans… Traceability is a major issue, covered with the generation of manufacturing books with the required information according to the control plans (material certificates, dimensional and electrical control tracks, manufacturing process parameters, welding and welders qualification records, leak test records…)
How will the ITER Poloidal Field Coils be manufactured?
Once the 1 100 tonnes of the stainless steel clad niobium titanium conductor arrive on the ITER site, in order to manufacture the European coils, they will progressively move from the external storage area to the manufacturing hub, where the winding and vacuum impregnation processes will be carried out. During the moulding stage, epoxy resin will be uniformly applied to help the layers of the conductor to bond tightly in order to create a coil known as double pancake. Then, a second impregnation process will take place to bond the stack of the double pancakes to form one complete massive coil.
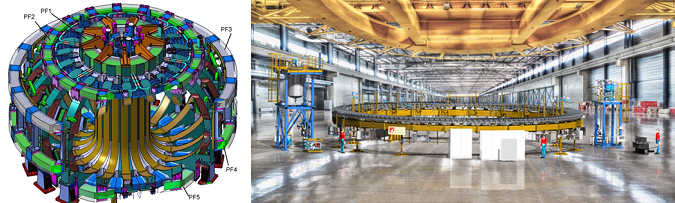